When deciding on the best method for producing plastic components, manufacturers often face the dilemma of whether to opt for thermoforming or injection molding. Both are popular plastic shaping techniques, yet they are fundamentally different in terms of the materials used, the processes involved, and the end products they yield. This article will explore both processes, highlighting their differences, advantages, and best-use scenarios to help businesses make an informed decision.
Overview of Thermoforming vs Injection Molding
Thermoforming is a manufacturing process that involves heating a plastic sheet until it becomes soft and pliable, then shaping it over a mold using vacuum or pressure. This process is ideal for producing relatively simple parts, including trays, packaging, and large components with low to medium precision.
In contrast, injection molding is a more complex process in which molten plastic is injected into a precisely designed mold cavity under high pressure. This method is highly effective for creating parts with intricate shapes and superior dimensional accuracy, often used in industries like automotive, electronics, and medical devices.
Why Choosing the Right Process Matters in Manufacturing?
The choice between thermoforming and injection molding has profound implications for both production efficiency and the quality of the final product. Selecting the correct process ensures that manufacturing costs remain manageable, product quality meets specifications, and production timelines are optimized. Making the right decision hinges on understanding the unique characteristics of each technique, including the materials, cost structures, and scalability considerations.
Overview of Thermoforming Process
How Thermoforming Works: The Basics
In thermoforming, the process begins with a flat plastic sheet, typically made from materials such as PVC, PET, or polystyrene. The sheet is heated until it reaches a pliable state, then placed over a mold. A vacuum or air pressure is applied to the softened plastic, forcing it into the mold’s shape. Once cooled, the formed part is trimmed to remove excess material. This process is fast and cost-effective, especially for low- to medium-volume production runs.
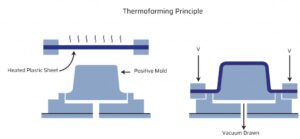
Materials Used in Thermoforming
Thermoforming utilizes a wide variety of thermoplastics, including materials like PVC, ABS, polycarbonate, and PETG. These plastics are ideal for the process due to their ability to soften when heated and retain shape once cooled. The choice of material depends largely on the desired attributes of the final product, including clarity, strength, flexibility, and heat resistance.
Applications and Industries Best Suited for Thermoforming
Thermoforming is commonly used in industries where large parts with relatively simple shapes are required. Typical applications include food packaging, trays, clamshell packaging, automotive parts, and appliance components. It is especially advantageous for producing large sheets or thin-walled parts, making it suitable for both consumer goods and industrial applications.
Overview of Injection Molding Process
How Injection Molding Works: The Basics
Injection molding involves injecting molten plastic into a mold cavity under high pressure. The plastic is typically heated to a molten state and then injected into the mold using a hydraulic or electric press. After the material cools and solidifies, the part is ejected from the mold. The process is highly precise, capable of producing complex shapes with tight tolerances and excellent surface finishes. It is well-suited for high-volume production runs.
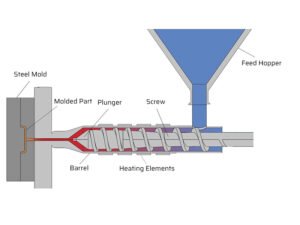
Materials Used in Injection Molding
Injection molding can utilize a broad range of thermoplastic and thermosetting materials, including polycarbonate, polyethylene, polypropylene, nylon, and various engineering plastics. The choice of material is critical in determining the strength, durability, and chemical resistance of the final product, with different plastics offering unique properties suited to diverse applications.
Applications and Industries Best Suited for Injection Molding
Injection molding is prevalent in industries where high precision, durability, and complex part geometries are required. It is commonly used for producing components in automotive, electronics, medical devices, consumer goods, and industrial machinery. The versatility and accuracy of the process make it the preferred choice for high-performance parts that demand consistency and detailed features.
Key Differences Between Thermoforming and Injection Molding
Cost Comparison: Which Process is More Cost-Effective?
Thermoforming generally offers lower upfront tooling costs, making it more cost-effective for small to medium production runs. The molds used in thermoforming are simpler and less expensive to produce, which is beneficial for companies with limited budgets or those needing to prototype quickly. On the other hand, injection molding requires more expensive molds and a higher initial investment, but it becomes more cost-effective at larger production volumes due to its ability to produce high quantities of parts with minimal waste.
Production Volume and Speed: Which Process is Faster?
Thermoforming typically offers faster production times per part, especially for larger and simpler designs. The heating and molding steps are less complex, allowing for quicker cycles. However, injection molding is far superior for high-volume production, where rapid part ejection and minimal cycle time are crucial. The speed of injection molding increases significantly with larger runs, although the setup time for molds can be longer.
Material Flexibility: Which Process Offers More Variety?
Injection molding provides a greater variety of material options, including specialized engineering plastics that thermoforming cannot accommodate. The wide range of materials available for injection molding allows manufacturers to select the best material for the part’s specific functional requirements, such as heat resistance, strength, or electrical properties. In contrast, thermoforming is more limited to less specialized thermoplastics, although it can still accommodate a diverse array of materials suited for less demanding applications.
Design and Complexity: Thermoforming vs. Injection Molding
Injection molding excels in creating parts with intricate geometries, thin walls, and detailed features. The high pressure used in the process allows for precise control over part dimensions, making it ideal for complex designs. Thermoforming, while capable of producing large parts, is better suited for simpler designs with less intricate detailing. The lack of high pressure in thermoforming limits its ability to handle highly detailed or complex parts.
Tolerance and Precision: Which Process Delivers Higher Accuracy?
Injection molding is renowned for its ability to produce parts with very tight tolerances and superior dimensional accuracy. The mold cavities are engineered to precise specifications, ensuring that each part produced is identical. Thermoforming, however, has a greater tolerance for variation due to the nature of the process. The vacuum or pressure used in thermoforming can result in slight differences in part thickness and shape, which may not meet the stringent requirements of certain industries.
Environmental Considerations: Waste Management and Sustainability
Both processes generate waste, but the types and quantities vary. Thermoforming typically results in scrap material when trimming parts, though this waste is often recyclable. Injection molding, on the other hand, can produce sprue and runner waste, which can be reused in subsequent cycles, reducing overall material waste. However, the energy consumption of injection molding tends to be higher due to the need for molten plastic and complex machinery.
When to Use Thermoforming vs. Injection Molding
Best Use Cases for Thermoforming: Thin-Walled Parts and Large Sheets
Thermoforming is ideal for creating large parts with simple geometries, especially when thin-walled designs are required. It’s commonly used in packaging, such as clamshell and blister packs, and for automotive interior components like dashboards and door panels. Additionally, thermoforming is well-suited for prototyping due to its low tooling costs and faster turnaround.
Best Use Cases for Injection Molding: High Precision and Complex Shapes
Injection molding is best for high-precision, high-complexity parts that require tight tolerances and intricate features. Its ability to produce a large volume of parts with consistent quality makes it ideal for industries like automotive, electronics, and medical device manufacturing. Injection molding is also the preferred choice for creating parts with multiple cavities, undercuts, or other sophisticated design elements.
Common Mistakes to Avoid When Choosing Between Thermoformed vs Injection Molding
Design Missteps That Lead to Costly Errors
One common mistake is underestimating the complexity of the design and the limitations of each process. Thermoforming is often chosen for its cost-effectiveness, but designers may not fully account for its limitations in producing intricate shapes or achieving high precision. Similarly, opting for injection molding without fully understanding the tooling and material costs can result in unnecessary expenses.
Underestimating Material Costs and Availability
Material selection is crucial in both processes, and underestimating the cost and availability of certain plastics can lead to production delays or unexpected costs. Both thermoforming and injection molding rely on specific grades of plastic, and sourcing these materials at scale can become a significant factor in the overall cost structure.
Choosing the Right Process for Your Needs
In conclusion, the choice between thermoforming and injection molding depends on a variety of factors, including production volume, part complexity, material requirements, and budget constraints. Each process offers unique advantages, and understanding these differences is essential for selecting the best method to achieve high-quality results. By carefully assessing the specific needs of a project, manufacturers can optimize their production methods for efficiency, cost-effectiveness, and product performance.