Thin wall injection molding is a specialized manufacturing process that focuses on creating lightweight plastic parts. This technique can produce parts that are not only lightweight but also cost-effective and efficient in material usage. In this post, we will explore thin wall injection molding applications and design tips.
What is Thin Wall Injection Molding?
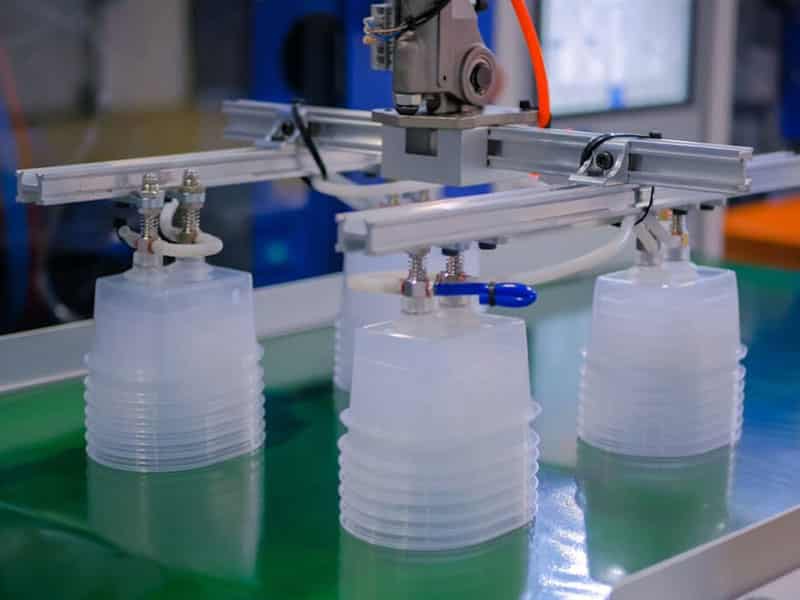
Thin wall injection molding is a specialized manufacturing process that focuses on creating lightweight plastic parts with wall thicknesses typically less than 1 mm. This technique enables manufacturers to produce thinner and lighter components without compromising structural integrity. This process can improve material efficiency and faster cycle time. However, the thin wall injection molding process is more complex than traditional injection molding. The thin wall injection molding requires higher pressure and faster molding speeds to ensure complete filling of the cavities and avoid defects. For example, a part with standard walls may need to be filled in two seconds, while the same part with 25% thinner walls may require a one-second fill time. The thin wall molding needs more design tips.
Thin Wall Injection Molding: Design Tips and Tricks
Designing parts for thin-wall molding requires careful consideration to ensure successful manufacturing and high-quality thin-wall plastic parts. Here are some key tips and tricks to keep in mind when designing thin wall parts:
1. Uniform Wall Thickness
In thin-wall injection molding, maintaining uniform wall thickness is critical to ensure even cooling and prevent defects like warping or sink marks. Variations in thickness can lead to differential cooling rates, causing internal stresses and part distortion. Designers should aim for wall thicknesses between 0.5 mm to 1.5 mm, depending on the material and part size. Thinner walls lead to faster cooling but may compromise strength. Maintain uniform wall thickness throughout the part to prevent uneven cooling and warping. However, it’s essential to balance thinness with the material’s flow properties and the part’s strength needs.
2. Optimize Cooling System
Incorporate cooling channels in the mold design, strategically placed to remove heat efficiently. Use conformal cooling channels that follow the contours of the part for optimal heat transfer. Consider using mold materials with high thermal conductivity, such as beryllium-copper alloys, to enhance cooling.
3. Optimize Part Geometry
Simplifying part geometry is key to successful thin-wall molding. Complex designs can hinder material flow and lead to uneven cooling, increasing the risk of defects. Using rounded corners instead of sharp edges helps reduce stress concentrations and improves material flow.
Incorporating draft angles is essential for thin-wall parts to ensure easy ejection from the mold. A draft angle of 1-2° is typically sufficient to reduce friction between the part and the mold, minimizing the risk of damage during ejection.
Adding ribs and reinforcements is an effective way to enhance part strength without increasing wall thickness. Ribs should be designed with a thickness of 40-60% of the main wall to avoid sink marks. Similarly, bosses should have thin walls and adequate draft angles to facilitate ejection and prevent defects.
4. Consider Material Shrinkage and Warpage
Choosing the right material is crucial for thin-wall molding. High-flow materials, such as polypropylene, ABS, or polycarbonate blends, are ideal because they can easily fill thin cavities without requiring excessive pressure. These materials have high melt flow rates (MFR), which ensure smooth flow and reduce the risk of incomplete filling. Additionally, incorporating flow-enhancing additives can further improve material performance, making it easier to achieve consistent part quality in thin-wall applications.
Anticipate and compensate for material shrinkage by designing the part slightly larger than the desired final dimensions. Incorporate ribs, gussets, or bosses to minimize warpage and distortion during cooling. Use simulation software to predict and analyze potential shrinkage and warpage issues before manufacturing.
Learn 6 common mistakes in plastic material selection and how to avoid them
5. Optimize Gate Design
Proper gate placement ensures even material distribution and minimizes pressure drops, which are critical for filling thin cavities. Smaller gates are often preferred to reduce shear stress and prevent material degradation. For larger parts, using multiple gates can help distribute the material more evenly, reducing the flow length and ensuring uniform filling. Careful consideration of gate size, location, and number is essential to achieve optimal results.
6. Optimizing Injection Parameters
Higher Injection Pressure: Higher injection pressures may be necessary to fill the thin cavities adequately. This helps avoid issues such as short shots or incomplete filling.
Faster Injection Speed: Faster injection speeds are often required to ensure that the molten material reaches all areas of the mold before it begins to cool. This is particularly important for parts with significantly reduced wall thickness.
Correct Temperature Control: Maintaining the right temperature for both the molten plastic and the mold is essential to achieve the desired flow characteristics and prevent defects such as warping or sink marks.
Learn more about the most common 8 injection molding parameters.
What Are the Common Applications of Thin Wall Injection Molding?
Thin wall injection molding is utilized across various industries due to its efficiency and ability to produce thin wall plastic parts. Here are some common thin-wall injection molding applications:
- Packaging
- Food Containers
- Bottles and Caps
- Consumer Goods
- Household Items: Such as storage containers, cups, and kitchen utensils.
- Electronics Housings
- Medical Devices
- Syringes and Vials
- Test kits
- Automotive Parts
- Interior Components
- Bumpers and Grilles
Conclusion
Thin wall injection molding offers numerous benefits that are vital in the contemporary manufacturing landscape. This process allows for the production of lightweight and efficient plastic components, significantly reducing material usage and costs while enhancing productivity. Erye Rubber and Plastic is a professional manufacturing partner that can help you through the injection molding process, from mold design to production. Contact us to start your injection molding project.